Planer thicknesser purchasing advice: how to choose the right product
- What you need to know
- There are planers for planing wood material, for reducing the thickness, as well as combination machines that perform both tasks.
- Combination units are recommended as soon as larger quantities of wood material are to be shaped.
- Large stationary units weighing several hundred kilograms are used primarily in the commercial sector.
- Compact, portable units are ideal for a home workshop with limited space.
- Since the passage determines how wide the wood to be planed can be, it should be as large as possible.
Woodworking at the next level
Anyone who has been involved in woodworking for any length of time knows how carefully the surface must be treated in many projects to achieve a satisfactory result: It must be smooth and straight, as well as constantly have the perfect thickness. A grinder is used for smoothing, and a planer for flattening. Instead of laboriously running a manual planer over the wood countless times, consider investing in an electric planer. Even greater ease of work are planers, where you only need to put the wood in the housing opening – the device will do the rest. With such a machine, you are independent of cuts from the hardware store, you can plane all the materials yourself and use them for your projects.
Such devices are available either as pure thickness planers, jointers or combined jointers-thickness planers. Pure thickness planers reduce the thickness of a workpiece, while jointers ensure that the sides of the wood have a right angle. The latter are used mainly for boards, planks and squared timber. If you want to machine a material from scratch, you must first dressit and then flatten it. For this reason, combined surface planers and thicknessers that perform both tasks can now be found in the trade, so that there is no need for two separate devices in a workshop. To switch between functions, they often have a folding mechanism.
How do planers work?
Surface planers are equipped with a take-up and take-off table, which guide the wood to be dressed under the cutterhead. This has one to four knives. The pick-up table in front of the cutter is usually slightly longer than the pick-up table behind the knives. To protect users from cuts, the cutter head is covered on both the front and rear sides. The correct angle can be set with the aid of a stop ruler.
Thickness planers have infeed and outfeed rollers. If you place a wooden beam or board on the passage leading to the knife shaft, it will come into contact with the feed roller, which is attached to the top of the housing and rotates on its own axis. This roller presses on the wood and transports it to the cutter by the rotation. The extraction shaft brings out the processed wood from the cutter. In addition, a pressure bar in front of and behind the cutter head ensure that the material does not slip.
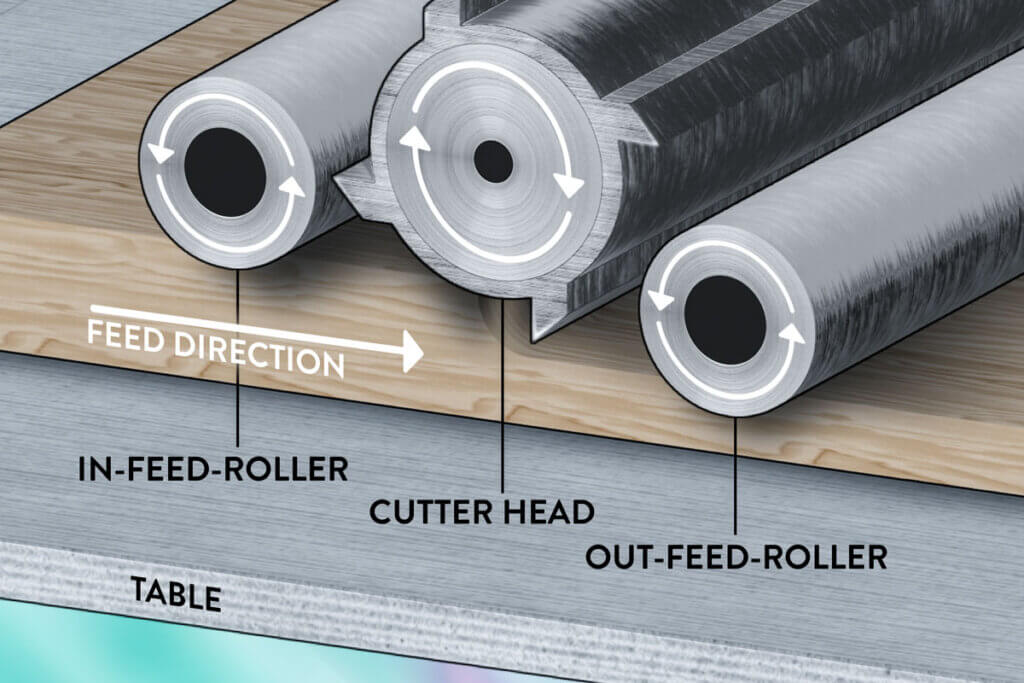
This is what matters when buying
Buying a planer depends on your crafting skills, the materials you use for your projects, and the space you have available. Experienced craftsmen have different requirements than those who are just starting to work with wood themselves.
Type of planer
Those with limited space or budget may wonder if it has to be the expensive combined jointer-thicknesser or if a pure thickness planer will suffice to machine workpieces. Basically, it depends on what materials you use and whether you need to dress them.
For small quantities of wood, a router table, hand plane or hand circular saw is sometimes all that is needed to create a right angle between edge and face. Since this method is impractical and time-consuming, it is not recommended for large quantities of wood. If you only want to thin glue-laminated boards, you can easily dispense with the dressing function. However, as soon as you want to shape larger quantities of solid wood, a combined planer is practical.
Large and efficient or compact and portable?
There are both compact planers and large, stationary models. Small planers can be stored in the workshop and transported to the place of use to save space. In addition, they usually only require conventional 230-volt mains power. This means that they can flexibly choose the place of use for the planer and do not have to follow a specific connection. However, the compact machines are usually not as wide as stationary models, which limits users in their choice of workpieces. You may need to join several narrower pieces together to make a wider one. The motor power is on average between 1,500 and 2,000 watts. This is easily sufficient for planing soft woods, but hardwoods such as oak or beech can cause problems.
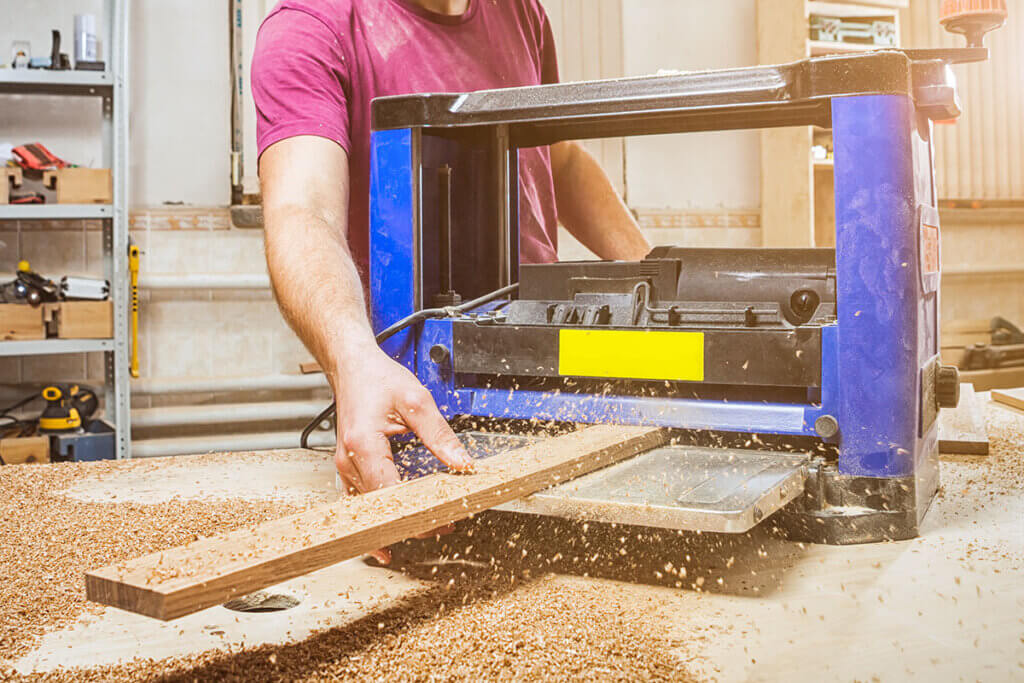
Stationary professional machines require a large workshop where they can stand in a fixed place. Unlike compact machines, mains power is not enough for them; instead, they need heavy current. Unless you already have a 400-volt power outlet in your shop, you will need to install it in order to use the machine. While compact planers often weigh between 20 and 40 kilograms, the weight of stationary machines is usually several hundred kilograms. With this equipment, even the processing of solid hardwood succeeds.
Material
High-quality planers are often made entirely of durable steel. Other metals such as die-cast aluminum are also used for the housing and mechanics. Impact-resistant plastic is also used for the housing, especially in compact machines. Therefore, they are significantly lighter than their larger counterparts. Dispensing and receiving tables ideally have a smooth metal surface to make it easier to move the wood.
Maximum planing depth
The planing depth or chip removal indicates how many millimeters the machine can lift in one pass. The maximum chip removal is usually between two and five millimeters. The higher the chip removal rate, the less often you will need to push the wood under the cutterhead to bring it to the desired thickness. It is practical if the depth is adjustable. This allows you to precisely adapt the chip removal to the material and the intended use.
Diffuser and workpiece dimensions
The machining width and height of a thickness planer determine how large the workpieces may be. In most cases, the height of the diffuser or the maximum material height is between 120 and 250 millimeters. For compact machines, about 150 millimeters is common.
For those who want to work both large and small pieces of wood, the opening can not be large enough. However, large machines with a price of more than 1,000 euros are not only very expensive, but also take up a lot of space. Even if there is enough money, models with a working width of more than 600 millimeters do not fit into the workshop of many DIY enthusiasts. In fact, 600 millimeters is typically the maximum depth of cabinets, and therefore the ideal size for furniture construction.
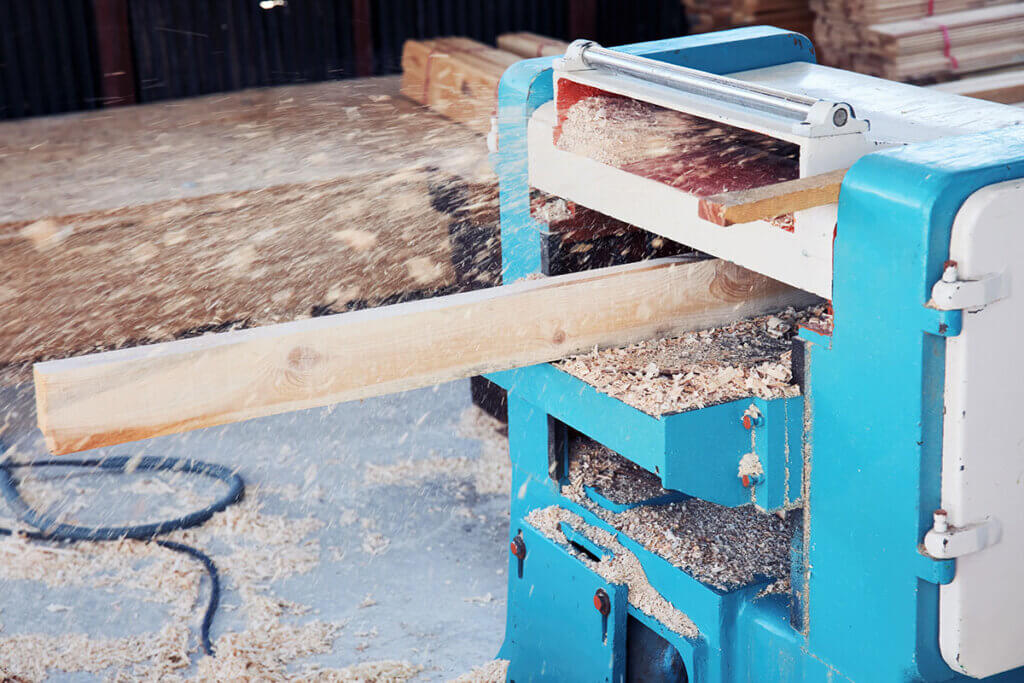
If setting up a planer with a clearance width of 600 millimeters is not possible, for example, due to space constraints, craftsmen will have to put two wooden boards together after planing to obtain the desired width. Here it is recommended to use a planer, where you subsequently have to join as few panels as possible. This would be a pass width of 310 millimeters. Those who work only narrow pieces of wood, can also choose a width of less than 200 millimeters. Portable planers usually start with a passage width of 120 millimeters and rarely reach 310 millimeters. That’s more reserved for the big, stationary machines.
Material feed
The material feed rate determines how long the planer needs for one working pass. It is given in meters per minute, so it informs how many meters of wood the machine can transport under the cutterhead in one minute. For those who do not have experience with planers, it is sometimes advisable not to take the device with the fastest possible material feed.
Instead of, say, eight meters per minute, choose a machine with a material feed rate of five meters per minute. Lower speed makes it easier for you to maintain control over the planing process. For experienced craftsmen recommend at least seven meters per minute.
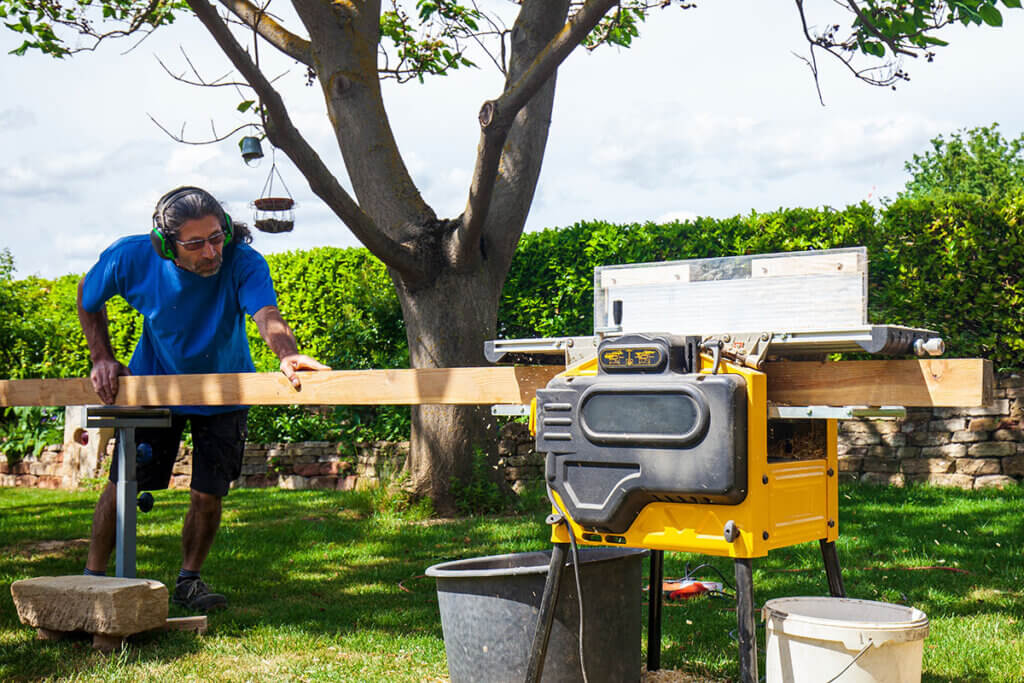
Number of revolutions
How fast the planer shaft rotates is indicated by the number of revolutions per minute. The radius of the cutter head can also be used to determine the circumferential speed or the cutting speed of the cutter head. However, even the number of revolutions helps to estimate the capabilities of a planer. The faster the cutter turns, the smoother and finer the surface will be after planing. Make sure that the number of revolutions is not too high for the material feed. If this does not transport the material fast enough, heat can develop at high rotational speeds.
Depending on the size of the cutterhead and the knives integrated in it, the recommended number of revolutions differs. Compact planers require higher speeds than large professional machines with up to four knives. The latter also achieve excellent performance with only 4,000 rpm. For small planers and cutters, a speed of more than 8,000 revolutions per minute is useful. There are also machines with a speed of more than 10,000 revolutions per minute, such as the compact thickness planer DeWalt DW733-QSwith two knives.
Planer knife
There are different planing knives and cutterblocks for sale. The knives themselves are usually made of high-speed steel, HSS steel for short, or carbide. While HSS steel is very sharp but not as robust, the opposite is true for carbide knives: They are more durable, but not as sharp as HSS steel knives. The knives have only a minor effect on the planing result. With HSS steel, at best, a somewhat smoother result can be achieved. More important is the underlying system. The three common types are strip planer knives, which are attached to the planer shaft with gibs, the so-called Tersa systemand spiral cutter shafts.
Strip planer knives are the standard system for planers. Some manufacturers use notches or grooves to attract customers to buy replacement knives. With strip planing knives it is necessary to adjust the height yourself. Depending on the product, this can be cumbersome.
The Tersa–System works with reversible knives and uses centrifugal force to effortlessly bring them into the correct position with millimeter precision. The knife change is quick and easy. Craftsmen only need to insert or clamp the knives in the designated place. This takes a few minutes. Tersa cutterblocksare mainly integrated in high-quality planers for the commercial sector.
Spiral cutter shafts consist of at least 48 helically arranged indexable inserts. As soon as a knife is damaged or worn, you can turn the cutter head and use another knife or replace it directly. It is not necessary to replace the entire cutterhead. Due to the spiral arrangement, the individual knives are always in the right position. However, the complete replacement of the knives is time-consuming and expensive. Finally, they need to buy 48 replacement blades and put them in place.
Planing safely
Three devices are available for covering the cutterhead of surface planers:
- a flap guard with wing strip
- a limb vibration protection
- a protective bridge
A flap guard is the simplest option. It is composed of several wooden flaps connected by means of hinges. A limb vibration guard releases the cutter head as soon as it comes into contact with the workpiece. However, large pieces may cause the guard to swing to the side early. Protective bridges are the safest protective device among the three methods. They release the knives only when the material touches a special stop. Otherwise, the cutter remains completely covered.
Another safety feature is the anti-kickback device. It consists of several steel links or grippers positioned below the blade flight circle. Furthermore, the securing should cover the entire width of the insertion opening. An overload switch is also one of the standard features,
Even with the aforementioned safety features on the planer, there is still some risk of injury to craftsmen. Planing produces a lot of wood chips and fine dust, which even the suction device of a stationary machine often cannot remove completely. Even a workshop vacuum cleaner, whose hose can be attached to many planers, sometimes reaches its limits. The fine dirt can get into the eyes as well as the lungs and cause damage. Safety goggles and a respirator mask protect against this.
Since most planers exceed 85 decibels in volume, hearing protection in the form of headphones or earplugs is essential to prevent permanent hearing damage. Cut-resistant gloves are also useful, as the hands come into direct contact with the wood to be planed.
Useful accessories
Table extensions are ideal for those who want to dress long workpieces. There are both extensions for a specific planer and those that are universal, for example, from the company Aigner. Not only do universal extensions come in a variety of lengths, but they can also be mounted on numerous, stationary planers to extend jointer tables up to 1.8 meters. To do this, hang the accessory in a steel rail and secure it with a clamping lever. A height-adjustable support leg provides stability. During assembly, it is important to work precisely so that the table extension is level, otherwise the workpieces cannot be planed straight.
Furthermore, several stops are practical, including an auxiliary stop that is already factory-fitted on many professional devices. This is also recommended for compact models, as it facilitates the dressing of narrow workpieces. In addition, the hands can be supported on it. After attaching it to the sash stop, you can fold it down if necessary. For those who want to process window and door rebates, it is helpful to have a rebate depth stop that can be adjusted continuously. To ensure that neither the material nor the planer is damaged, the surface of the pick-up and delivery table should be as smooth as possible. You can ensure this with a special lubricant for machine tables. This is available in liquid and dry form. Liquid lubricant is usually available in spray bottles, which makes it difficult to dispense. However, it is possible to spray it on a cloth first and then rub the table with it without any problems. Make sure that no lubricant gets on the infeed rollers, as they have to grip the wood.
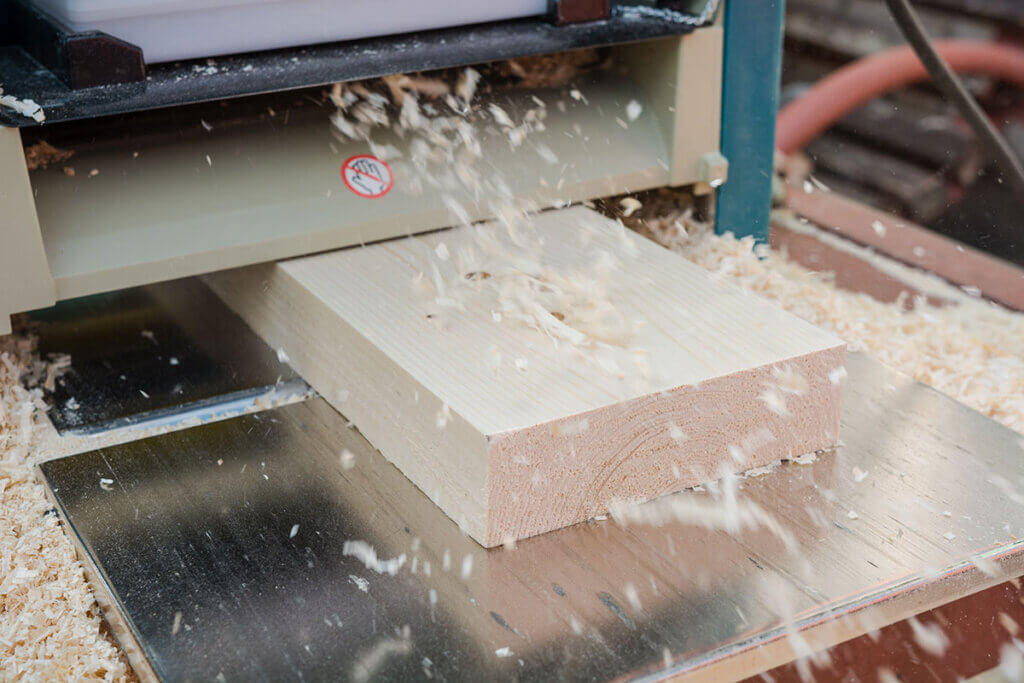
Image 1: © FinalCheck | Image 2: © Виталий Сова / stock.adobe.com | Image 3: © Cagkan / stock.adobe.com | Image 4: © ImagESine / stock.adobe.com | Image 5: © Sergey_Siberia88 / stock.adobe.com