Plasma cutter purchasing advice: how to choose the right product
- What you need to know
- Plasma cutters are designed for quickly and precisely cutting conductive metals.
- Plasma can be as hot as 54,000 °F (30,000 °C) when slicing through metal.
- There are a few different types of plasma cutter, depending on whether they are for home users, professionals, or industrial applications.
- Basic plasma cutters for home use start at around $200.
Powerful tools for cutting metal
Plasma cutters are powerful, versatile tools used to cut conductive metals like steel, copper, aluminum, and stainless steel quickly and precisely. They have been around for a while, and it’s now impossible to imagine metalworking without them. Cheap plasma cutters suitable for home use are great for beginners and hobbyists, but they are very different to expensive ones designed for professionals and those working in factories. In this article, we will detail the different types of plasma cutters available on the market, and what to look out for when choosing one.
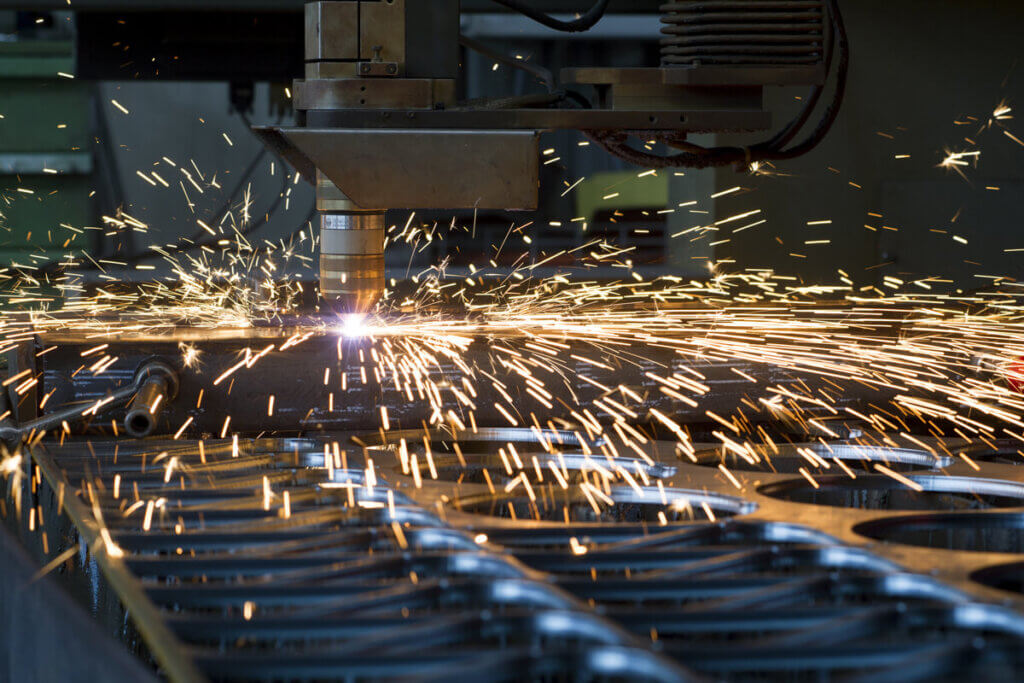
How do plasma cutters work?
Plasma cutters work by generating a jet of high-temperature plasma to cut through metal. They operate at a much higher temperature compared to gas cutting torches – plasma can be as hot as 54,000 °F (30,000 °C). When using one, you guide the plasma jet via a nozzle. This means that plasma cutters can be easily controlled by a hand or a machine, and the nozzle can be moved in any direction. This makes cutting metal fast and extremely precise, even when it is extremely thick. It also makes cutting curves and irregular shapes easy – something that is quite difficult to do with gas cutters. Plasma cutters offer a high degree of flexibility when it comes to cutting metal, making them a versatile tool for metalworking both at home and in industry.
What is plasma?
As a broad rule, materials can exist in three states of matter: solid, liquid, and gas. The state of a material is determined by temperature and pressure. For example, water is liquid at normal atmospheric pressure between 32 and 212 °F (0-100 °C). If the temperature goes below 32 °F, it will freeze solid, and if it goes above 212 °F, it turns into gaseous steam. If you continue to heat gas further, it begins to take on free charge carriers, negatively charged electrons, or ions. This highly energized gas mixed with an electrical charge exists in a fourth state: plasma.
Plasma cutters use DV voltage from a welder to generate a strong electrical arc. This arc runs between the workpiece (which functions as the anode) and the cathode at the tip of handle. The energy is focused and directed through a copper nozzle which shoots out superheated plasma between 27,000 and 54,000 °F (15,000-30,000 °C). This plasma vaporizes the metal it touches, and the vapor created is blown away by a compressed gas jet.
Most plasma cutters use compressed air as the gas source. A lot of devices don’t have an integrated compressor, so you’ll need to get your own – something to consider before making a purchase. To get the best results and avoid any jagged edges or corrosion, you can use special protective gas provided your cutter is compatible.
Industrial plasma cutters
- Can cut metal up to 8 inches (20cm) thick
- Usually more complex to operate
- Require more accessories
Home plasma cutters
- Can cut up to half an inch thick metal (12mm)
- Simple to use
- Generally less accessories required
Since plasma is so hot – by comparison, welders operate at 5500 °F (3000 °C) – it can easily cut through thick sheets of metal. Due to this, plasma cutters are extremely useful for producing metal pieces in factories. They cut quickly, so bring down production costs. Likewise, they are great on construction sites and metalworking workshops because of their efficiency and speed.
Overall, plasma cutters are a great option for anyone who wants to cut metal accurately and precisely – even if it’s just in a home workshop. Before buying, you need to consider how much power you’ll need. If you only reckon you’ll need to cut thinner sheets – up to half an inch thick (12mm) – then a base model will be perfectly fine.
Can you cut non-conductive materials with plasma cutters?
The answer to this question depends on the type of plasma cutter you have – namely, whether it has a transferred or non-transferred arc. When people talk about plasma cutters, they are usually referring to transferred arc cutters. As the name suggests, this is where the flow of electricity is transferred from the tip of the nozzle to the piece of metal being worked on. These machines require the metal to conduct electricity. However, you can also get non-transferred plasma cutters. These have both anode and cathode in the handle, which means the material being worked on doesn’t need to conduct electricity. Non-transferred arc plasma cutters can be used to cut non-conductive materials such as concrete or glass. They are mainly designed for industrial rather than home use.
HF or lift-arc ignition?
Plasma cutters can also be categorized by the way in which their ignition system works. The two main ignition types are high frequency (HF) and lift-arc. HF ignition is technically more sophisticated. With this method, the arc is created at the touch of a button using a high-frequency current. While it is more sophisticated, you can still find HF ignitions on cheaper devices. A lot of other devices have a simpler lift-arc ignition instead. Here, the arc is created by briefly placing the handpiece with the current-carrying electrode on the metal work piece and then lifting it off. The technique is less convenient, but just as reliable.
Types of plasma cutter
Apart from categorizing plasma cutters based on transferred and non-transferred arcs, or based on their ignition systems, they can also be grouped based on other features.
Cutting power
Industrial plasma cutters can cut metal up to 8 inches thick (20cm) without a hitch. Home plasma cutters can usually cut up to half an inch thick metal, which should be plenty for hobbyists. If you want to cut anything thicker, you’ll need a more powerful machine which will of course cost more.
Gas and gas mixture
Most simple plasma cutters are designed to be used with compressed air. Higher-cost machines can also use nitrogen (or other suitable gases) to produce a cleaner cut. Top-of-the-range professional machines use a mixture of gases such as argon and hydrogen which make the hottest plasma. They are expensive to buy and expensive to run, so are mainly used by professionals in industrial settings.
Integrated or external compressor
Plasma cutters with an integrated compressor are usually more convenient to use than those that require an external one. For example, having a built-in compressor means that it will have the correct power output for your cutter – no need to mess around finding a compatible compressor. If you do need to get an external compressor, the specification to look out for is the effective delivery volume rather than the air discharge.
Weight
If you’re planning on moving your plasma cutter around (say, to different building sites), then pay attention to the weight. This is of course unimportant if you’re planning on keeping it permanently in one place.
Cooling and power requirements
If you have a home workshop, it’s a good idea to go for a plasma cutter that can be powered from a standard power outlet. Other devices need a special high-voltage connection. For plasma cutters with a relatively low cutting power and amperage, air cooling will be enough. For more powerful machines, you will need water cooling.
Hand-guided or machine-guided
For home users, having a hand-guided plasma cutter should be plenty. Machine-guided models are usually designed for industrial use, where the highest level of precision is required.
How much training do you need?
The simple answer is not too much – in fact, they are easier to use than welding machines. This said, plasma cutters are dangerous, so you should take the necessary safety precautions. Strong electric currents, sparks, steam, and extremely high temperatures can all cause serious injuries or even death. Follow all the instructions given in the manual, even if you’re experienced with other tools.
If you’re a complete beginner, it’s a good idea to get someone with experience to give you an introduction to safely assembling, using, and disassembling your plasma cutter. As always, your first few tries probably won’t produce the results you want, but keep trying.
Choosing the right plasma cutter
When picking a plasma cutter, you need to ask yourself a couple of questions: how often will you be using it, and what kind of accessories do you need? The answers to these two questions should determine what kind of money you should spend on getting a plasma cutter with the right kind of performance for your needs. Some accessories are essential for safe use, others are optional. When making a purchase, make sure to check what accessories as included. Sometimes, what looks like a good deal will disappoint, as you’ll have to buy essential extra accessories.
What to look out for when buying
Plasma cutters are high-precision machines that generate extremely high temperatures when in use. This can be dangerous, so only buy a plasma cutter with a seal of approval for safety. Well-made plasma cutters are available at competitive prices. Some bargain bin machines are often not only less durable, they can also be unsafe.
Go for a plasma cutter with the right power output for your needs. Base models should need about 40 amps for simple cutting jobs. If you want to cut thicker metals, then make sure your plasma cutter can do it beforehand. Depending on the model, plasma cutters are able to slice through metal up to 1.5 inches thick (4cm). The other important things to check are the ignition power and the open-circuit voltage. The open-circuit voltage needs to be at least 50 volts for the ignition to work properly.
If you want to weld as well as cut, you can get combination machines. Another small thing that makes a big difference is checking if the cables are long enough. It can get very frustrating if your cables are too short.
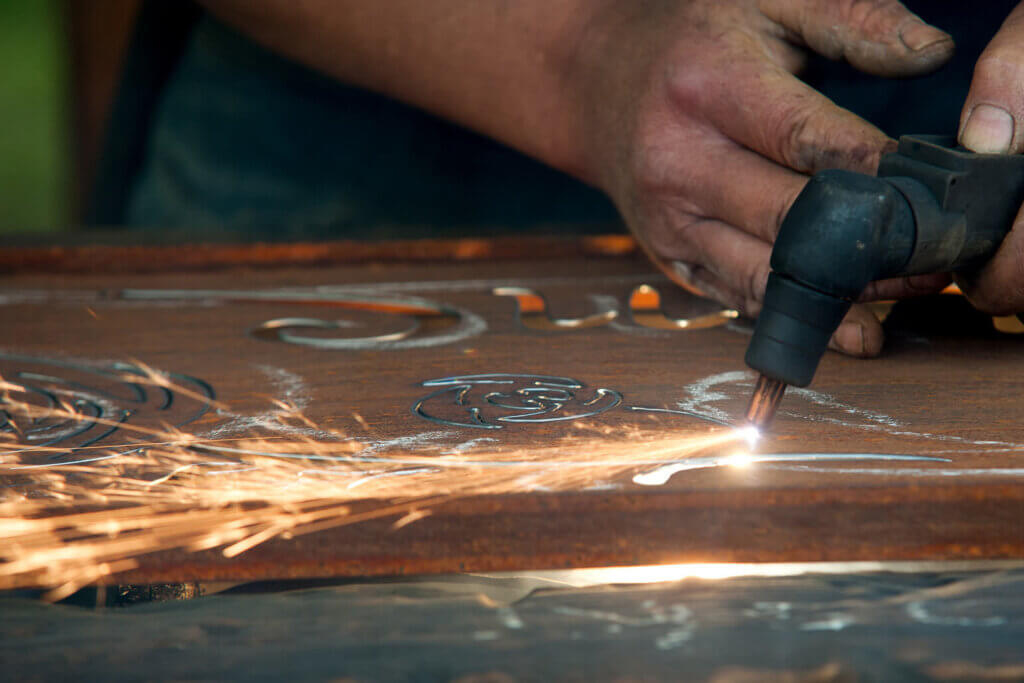
What are the essentials?
Plasma cutters need high-pressure gas to work. In order to get this, they need a compressor to produce pressurized air. If the model you go for doesn’t have an integrated compressor, then you’ll need to buy one extra. Another thing to check is the cooling system. Lower powered models (anything under 225 amps) will be fine with fans, but anything higher will need water cooling. Some models come with a cooling system, but make sure to check.
Usage tips
If you’re a beginner, or if you’re planning on using your plasma cutter infrequently, you’ll be perfectly happy with a simple model. They are easy to learn as they are simple to use.
Additional features and extra accessories which improve the cutting quality and speed only become important when you’re trying more advanced cuts. When doing more complex work, having a more complicated machine can really help as it is more versatile. For example, if you’re able to regulate the current and cutting speed, you can have more control. Units with a higher amperage can cut thicker and more conductive metals than units with a lower amperage.
Safety essentials
To use your plasma cutter safely, there are a few things you will always need. These include: a welding jacket, helmet, goggles, gloves, and a respirator mask. The surface you’re cutting on also needs to be fireproof. A spark protection mat is also important for preventing any fires. As a general rule, you should only use a plasma cutter in a well-ventilated room without any hazards.
Care tips
Compared to other cutting machines, plasma cutters don’t wear out as much with normal use. The main thing to watch out for is not to get any of the components oily or dirty. Some parts like hoses and nozzles are cheap and easy to replace. The main thing to consider is that you’ll need to get compatible components. Ideally, go for original replacement parts directly from the manufacturer, otherwise you can risk damaging your machine.
For more complex issues, always send your plasma cutter to a professional and let them fix it. It’s always best to have your plasma cutter fixed by the manufacturer. If you open your cutter yourself, you can void the warranty.
A lot of plasma cutters need additional cooling after use. Make sure to keep the device switched on for a while after you’re finished cutting.
Things to avoid
It might seem obvious, but never use a plasma cutter for anything other than its intended use. This will be clear in the instruction manual. Don’t, for example, use a plasma cutter to thaw cold pipes.
Important questions and answers
Here, you will find the answers to some of the most common questions regarding plasma cutters.
1. Whom are plasma cutters for?
Thanks to prices becoming more affordable, plasma cutters aren’t just for professionals any more. If you’re a hobbyist and only want to sometimes cut metal, you can get a basic model. If you’re going to be cutting a lot, then go for a more advanced machine.
2. Is it worth buying a budget machine?
Absolutely. After all, there are lots of high-quality models available at reasonable prices.
3. Can you get mobile plasma cutters?
Yes. They are great if you need to do any cutting outside of your workshop.
4. Which metals can I cut?
Any metal that conducts electricity can be cut with a plasma cutter. This includes metals like aluminum, steel, brass, copper, and iron.
Conclusion
Plasma cutters are a popular option with professionals and hobbyists wanting to cut metal. Entry-level devices with solid performance are available for relatively cheap nowadays, and if you want, you can always go for more expensive models with more accessories and features.
Image 1: © werbefoto-burger.ch / stock.adobe.com | Image 2: © haitaucher39 / stock.adobe.com